Kevin Brennan outlines how Lean and Six Sigma process management systems could be changed to redefine waste in ways that capture environmental impacts. These models historically seek to eliminate waste in production processes by defining it as anything that does not contribute to increasing customer value. Brennan argues that this customer-centric definition of waste should be broadened to recognize that a focus on customer value leads to practices that reduce environmental quality.
Article
Can Lean Practices Save the Planet?
Posted May 23, 2022 | Sustainability | Leadership | Amplify
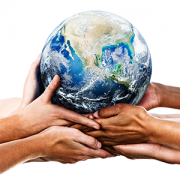
Don’t have a login?
Make one! It’s free and gives you access to all Cutter research.