Carl Faulkner presents a mining industry case study with a focus on data collection, integration, and storage challenges. The article includes lessons learned from the application of a solution designed to facilitate user-friendly access to digital twins as well as the importance of connecting digital twins to other business systems to get the most value.
Article
Digital Twins Unlock Business Value for Western Australian Mining Industry
Posted April 30, 2023 | Technology | Amplify
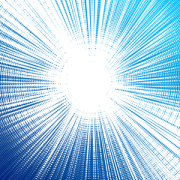
Don’t have a login?
Make one! It’s free and gives you access to all Cutter research.