In this Executive Update, we explore taking a process perspective to show how concepts such as sustainability and the circular economy look in the physical world. Making these concepts concrete reveals a singular criterion for achieving a circular economy: every output generated by every process should have a consumer who uses it productively. This criterion provides managers with actionable steps and ways to measure their organization’s progress toward sustainability.
Executive Update
Rethinking Sustainability: A Process Perspective
By Deishin Lee
Posted May 4, 2022 | Sustainability | Leadership |
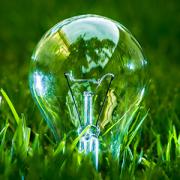
Don’t have a login?
Make one! It’s free and gives you access to all Cutter research.