We do not think and talk about what we see; we see what we are able to think and talk about.
— Edgar H. Schein, Humble Inquiry: The Gentle Art of Asking Instead of Telling
If we think about hierarchies, we will see their effects and try to improve them. If we instead think about value streams, we will see the effects of value streams and try to improve them. Hierarchies are a structure we use to organize our people; value streams represent the actual work we’re doing. Let’s explore the difference that shifting our focus creates.
The first thing to notice is that our work cuts across the organization and, therefore, across management hierarchies. If we look at workers involved in creating a product, they almost always report to several people. This requires the alignment of many people, often with disparate motives. Managing the work instead of the people creates an opportunity for better alignment.
Managing Within a Hierarchy
Hierarchies tend to have those responsible for the hierarchy manage the people under them to ensure they are:
-
Working on the right things
-
Working well
-
Fully occupied
This seems so natural we don’t even think about it. But it means the focus is on the people in the silo, not the workflow cutting across the silos. This results in delays when handoffs are made between silos.
Consider how focusing on silos affects value delivery. If we attend to silos and demand that managers lower costs, they will focus on doing their work more efficiently. However, this may lower the overall efficiency of creating value. W. Edwards Deming once remarked:
A system must be managed. It will not manage itself. Left to themselves, components become selfish, independent profit centers and thus destroy the system…. The secret is a cooperation between components toward the aim of the organization.
Reflect for a moment on projects you’ve seen in the past. Using Table 1, we can look at the people doing the work and the work itself (when it is being worked on and when it is waiting to be worked on).
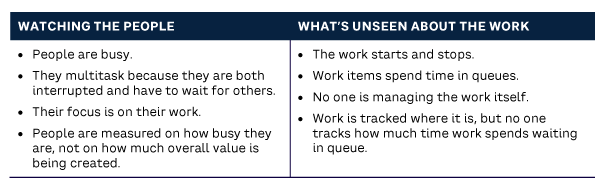
When we look at the people doing the work, we focus on a small part of the workflow. We tacitly assume that improving each step improves overall productivity. But this means ignoring the cost of handoffs and the waste due to slow feedback. It also makes it costly to pivot quickly.
Attending to value streams forces us to look at how long it takes to go from concept to consumption. Because people are busy and working on many things, projects often take longer than if people focused on just one project. We irrationally allow less important projects to slow down essential ones by having people work on both simultaneously.
Many people point to multitasking as a significant cause of waste. It is a significant one, but not the key one. Consider the cause of multitasking (people working in multiple value streams). People are being interrupted and are interrupting others. This results in work waiting in queues. While multitasking may cause a 10%-20% drop in efficiency, work waiting in queues creates unplanned work in the form of fixing bugs, working on the wrong things, rework, and so forth, which is much more costly.
Focus on Delays, not Eliminating Waste
Business leaders talk a lot about eliminating waste, but this mantra comes from the manufacturing environment where we can easily see waste. As a car is being built, mistakes are visible. In knowledge work, the situation is completely different. First, we can’t see everything and often don’t know when we have an error. Second, things like design and planning are not wasteful as they are often considered in manufacturing, causing a lack of agreement over what waste is.
With a bit of reflection, we can see that almost all the waste of product development stems from delays in workflow. In particular, when an error is made but not quickly detected, it usually takes more time to fix the error while increasing its impact. When there is a significant delay between when information is obtained and used, it can make the information less useful. This is yet another reason for quick feedback and reduced delays. The mantra needs to change from “eliminate waste” to “eliminate delays in the workflow.” Squeezing out delays also, obviously, shortens time to market.
[For more from the author on this topic, see: “Why Leaders Should Focus on Value Streams.”]